ROBOTIC PERFORMANCE
AT ITS BEST
Who we are
Where Robotics Meets Reliability –
Your Service Partner for Tomorrow
Robotics Service is dedicated to assisting system integrators and end users in optimizing the performance of their automation lines. In more than 20 years of experience we have empowered numerous customers to achieve peak efficiency and excellence in their automated processes.
We are a proud member of Efort Group, a globally trusted name in the production of robots. Our worldwide presence enables us to provide exceptional service on a global scale. Moreover, our team of highly skilled technicians stands as a testimony to our commitment to excellence and ensures that we meet the various needs of our customers with precision, creativity and expertise.
our service
Robotics Service has become a trusted partner for its customers, providing high-quality solutions in every area of industrial robotics.
In a world where industrial robotics is taking on an increasingly central role, maintenance and service are essential to ensure uninterrupted operations. Robotics Service, backed by its experience and expertise, is proud to offer a full range of services to meet our customers’ needs.
Service Management
Managing a service dedicated to industrial robotics requires state-of-the-art tools and processes. At Robotics Service, management is not just a process, but a philosophy.
- Ticket Generation and Management: an integrated system that allows our customers to report and monitor their needs in real time, ensuring timely intervention.
- Automatic Offer Compilation: thanks to our platform, we can generate offers accurately and quickly, responding promptly to customer requests.
- Accurate Cost Estimation: transparency is crucial. We provide clear and detailed estimates, ensuring a full understanding of cost items.
- Digital Log Reporting: all interventions, activities and updates are documented and made available in digital formats for easy consultation.
- Maintenance Contract Management: from maintenance contracts to warranties, every detail is taken care of, ensuring clarity and compliance.
- Service Contract Management: management and supervision of the terms and conditions of service contracts with customers.
- Warranty Management: management of warranty terms for products or services.
- Intervention Management: process of organizing, scheduling, and carrying out interventions or repairs.
- Remote Service Management: management and remote provision of services, using digital tools and technologies.
- Workload Planning: effective planning and distribution of work among team members.
Our approach to service management is the result of years of experience and innovation, aimed at offering our customers a flawless and reliable service that always meet their expectations.
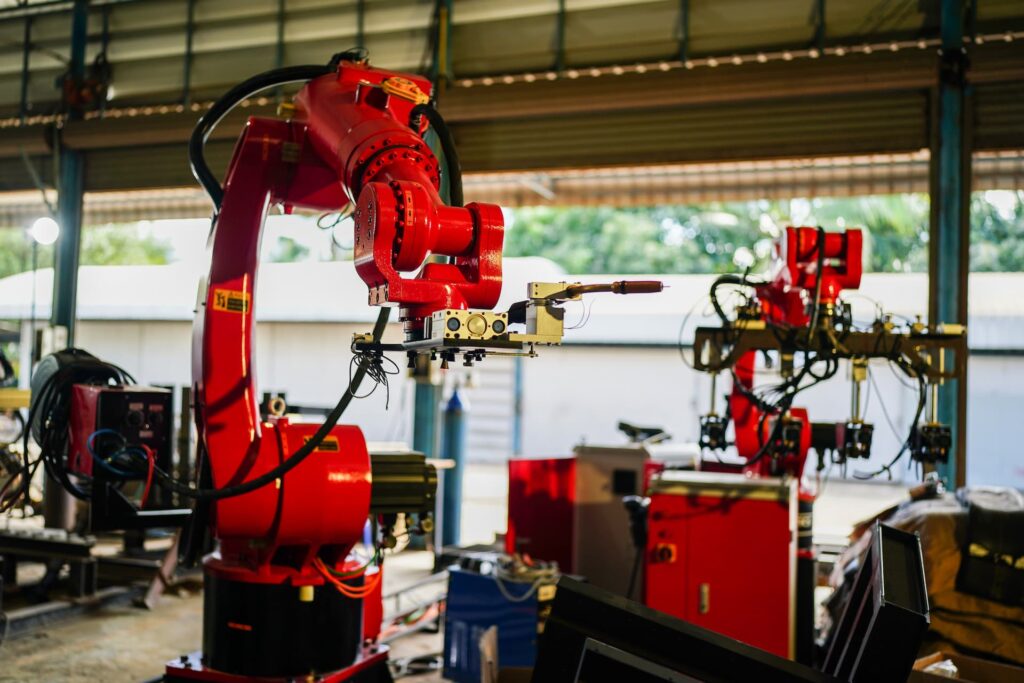
our expertise
Software
Our expertise in the software field ranges from PLC/HMI programming to robot programming support. We have partnerships with global leaders, such as: Siemens, Phoenix Contact, Omron and ABB. We are also specialists in device management and leaders in vision system applications.
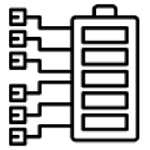
PLC/HMI Programming
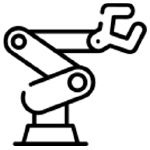
Robot Programming Support
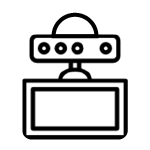
Device Management
Mechanics
Mechanics is the beating heart of every industrial robot. At Robotics Service, we not only take care of robot assembly and disassembly, but also provide essential services, such as: set-up and greasing of gears, as well as training on robot maintenance and calibration.
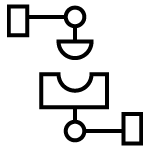
Robot Assembly & Disassembly
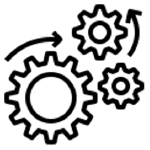
Gear Set-up and Greasing
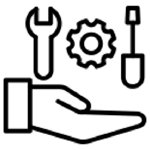
Robot Maintenance & Calibration Training
Electrics
The accuracy and reliability of a robotic system also depends on its electrical components. We offer services such as: failure list drafting, motor replacement and replacement of electric motors and encoders.
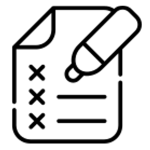
Failure List Drafting
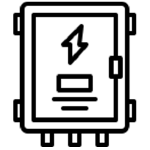
Motor drive replacement
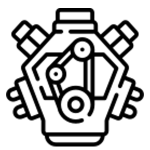
Electrical motor & encoder replacement
our Team
Our technicians represent the best in industrial robotics. Each skill reflects the dedication, training and experience of years of work in the field, ensuring high quality and professionalism to our customers.
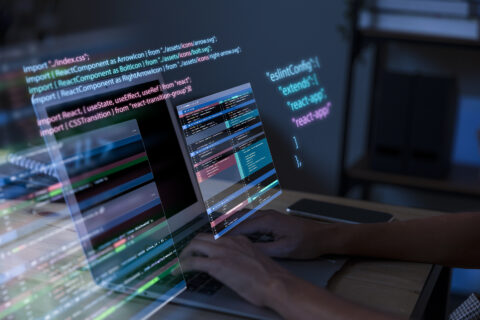
Robot programmer
- Man-machine programming interface: PCI, HMI, teach pendant
- Programming: standard settings, code programming information, standard parameters, machine alarms
- Robot programming: programming language, painting line details, details of robot path and routine, HW safety configuration, SW safety configuration
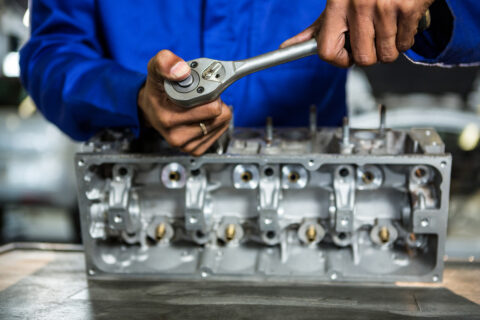
Mechanical Installer
- Robot assembly and disassembly
- Gear lubrication instructions
- Gear configuration instructions
- Training to move the robot to maintenance position and to restore the original programme
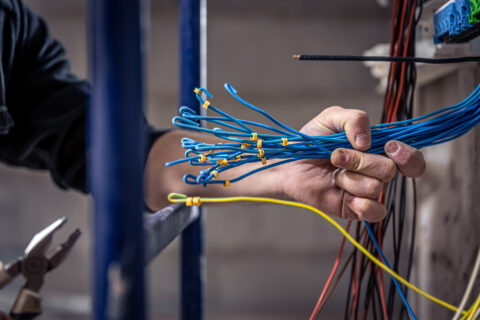
Electrical Installer
- Fault list drafting
- Procedures to replace the motor drive
- Procedures to replace the electrical motor and encoder
- Training to move the robot to maintenance position and to restore the original programme
Contact us
Robotics Service S.r.l.
25045 Castegnato (BS) - Italy
+39 030 2141193
+39 030 2141194
Fax: +39 030 2141195
General: info@robotics-service.it
PEC: evolut@pec.it
Sales: sales@robotics-service.it
Administration: fatture@robotics-service.it
Assistance: performance@robotics-service.it
Purchase: buyer@robotics-service.it